WS4 FUEL PRESSURE AND FLOW (PETROL ONLY)
The task to be done was to check the fuel pressure in the fuel rail on a toyota 4A-FE motor, this is done to make sure that everything is working properly so that the correct amount of fuel is delivered to the motor. These techniques can be used in engine diagnosis.
The first task to be done was to attach a fuel pressure gauge, but since a fuel pressure gauge was already installed this step was not necessary. Next the fuel pressure in the fuel rail had to be measured with the engine off, the reading I got was 35 PSI, the reason that pressure is needed in the fuel when the engine is off, is so that the engine starts quickly after its been at rest, and so that the engine does not need to be cranked over for a long time to build up the pressure again so that it can start. The reading of 35 PSI is a good reading as this is a good pressure to allow the fuel to atomize properly when it is injected into the combustion chamber. A bad reading would be a low reading something lower than 20 PSI this could indicate a fault with the fuel pressure regulator allowing to much fuel past suggesting that it is not shutting off the fuel return line completely when there is no vacuum being applied and this would cause the fuel pressure to drop.
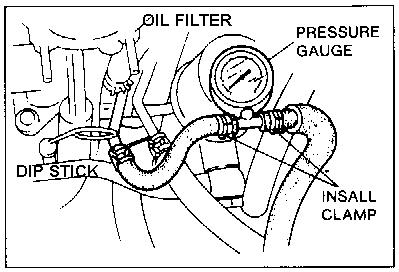
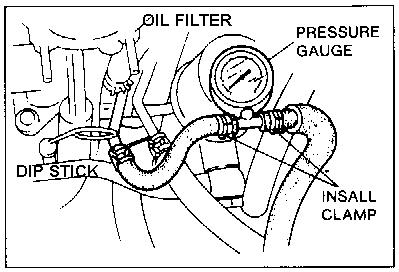
http://www.rx7.org/Robinette/images/fuel_gauge.gif
Next the fuel pressure was measured with the engine on but at Idle, the reading I got was 38 PSI which is a good reading as the pressure has increased, as now fuel demand is needed and higher pressure is required for fuel atomization. A bad reading would be anything less than 25 PSI this could be caused by a faulty fuel pump which is not pumping enough fuel to maintain correct fuel pressure. Or a faulty fuel pressure regulator which would cause the same problems as with the engine off fuel pressure test above.
The next test was to measure the maximum fuel pressure that can be attained, this is only done for a brief moment as damage can occur if its done to long. To attain maximum fuel pressure a clamp is used to clamp the fuel return line this is done make sure that the fuel pump is working properly and to check whether there are any leaks. The reading I got was 80 PSI which is a good reading, the fuel pressure rapidly increased to 80 PSI, this indicates that everything is working as it should. A bad reading would be one where the fuel pressure does not increase rapidly indicating a problem with either the fuel pump or the fuel pressure regulator.
The next test was to measure the fuel pressure at full throttle this is done by disconnecting the vacuum line to the fuel pressure regulator. This partially closes the fuel return line so that some fuel can return to the fuel tank but allows fuel pressure to increase since fuel demand is higher and the same fuel pressure as Idle would not be enough fuel under full throttle conditions meaning that the engine is running lean and it would be lacking in power. The reading I got was 48 PSI which is a good reading as fuel pressure has not increased to much but enough to allow the engine to keep running smoothly. Then reconnect the vacuum line after the test has been completed.
The last test was to measure the residual fuel pressure, this is done by switching off the engine for 5 minutes then taking the reading. The reading I got after 5 minutes was 42 PSI this is a good reading as the fuel pressure does increase slowly for a while then after a few hours it will slowly decrease. A bad reading would be anything under 25 PSI after 5 minutes as this could indicate that the fuel pressure regulator is faulty and is not maintaining correct fuel pressure after the engine has been switched off.
This is one of the main ways that you can check that the fuel system of the car is working properly.
The last part of the test was to answer some questions.
1) Explain why it is important to know a vehicles fuel pressure/flow?
-It is important to know a vehicles fuel pressure as correct fuel pressure is needed to allow for the correct amount of fuel to be injected into the combustion chamber. To much fuel pressure would mean that to much fuel is being injected and the engine would be running rich causing increased fuel consumption, if the fuel pressure was way to high like 80 PSI in the max pressure test that would cause what is known as dripping injectors. This is when the fuel pressure is so high that the fuel drops down in droplets and does not atomize properly causing a lot of unburnt fuel, also when the engine is off the fuel could drip past the injectors meaning that the engine is hard to start since it has essentially flooded itself. If the fuel pressure was to low then the engine would run lean making it lack in power and possibly run roughly.
2)Describe the symptoms a vehicle would give with each case.
LOW FUEL PRESSURE: The engine would run lean as it is not getting enough fuel, it may not idle properly and the revs could be to low due to there not being enough fuel to combust and this could cause the engine to run roughly during acceleration as there is not enough fuel to allow combustion to take place properly.
LOW FUEL FLOW: Could be caused by a faulty fuel pump which is not pumping enough fuel, this may not have any affect at Idle as there is enough fuel but as engine load and revs increase there is not enough fuel for the engine and this could cause to run rough as there is not enough fuel to efficiently combust.
HIGH FUEL PRESSURE: Fuel pressure regulator could be faulty causing dripping injectors if it is pressurizing the system to highly otherwise the engine would always be running rich causing increased fuel consumption.
FAULTY FUEL PRESSURE REGULATOR: Can cause dripping injectors which can cause hard starting since the motor has essentially flooded itself as fuel could get past the fuel injectors when the engine is off. Fuel could leak into the intake manifold causing a rich mixture. This could help during cold starts like a choke but hinder the ability for hot starts.

http://codinghorror.typepad.com/.a/6a0120a85dcdae970b0128776ffac2970c-pi
The last test was to measure the residual fuel pressure, this is done by switching off the engine for 5 minutes then taking the reading. The reading I got after 5 minutes was 42 PSI this is a good reading as the fuel pressure does increase slowly for a while then after a few hours it will slowly decrease. A bad reading would be anything under 25 PSI after 5 minutes as this could indicate that the fuel pressure regulator is faulty and is not maintaining correct fuel pressure after the engine has been switched off.
This is one of the main ways that you can check that the fuel system of the car is working properly.
The last part of the test was to answer some questions.
1) Explain why it is important to know a vehicles fuel pressure/flow?
-It is important to know a vehicles fuel pressure as correct fuel pressure is needed to allow for the correct amount of fuel to be injected into the combustion chamber. To much fuel pressure would mean that to much fuel is being injected and the engine would be running rich causing increased fuel consumption, if the fuel pressure was way to high like 80 PSI in the max pressure test that would cause what is known as dripping injectors. This is when the fuel pressure is so high that the fuel drops down in droplets and does not atomize properly causing a lot of unburnt fuel, also when the engine is off the fuel could drip past the injectors meaning that the engine is hard to start since it has essentially flooded itself. If the fuel pressure was to low then the engine would run lean making it lack in power and possibly run roughly.
2)Describe the symptoms a vehicle would give with each case.
LOW FUEL PRESSURE: The engine would run lean as it is not getting enough fuel, it may not idle properly and the revs could be to low due to there not being enough fuel to combust and this could cause the engine to run roughly during acceleration as there is not enough fuel to allow combustion to take place properly.
LOW FUEL FLOW: Could be caused by a faulty fuel pump which is not pumping enough fuel, this may not have any affect at Idle as there is enough fuel but as engine load and revs increase there is not enough fuel for the engine and this could cause to run rough as there is not enough fuel to efficiently combust.
HIGH FUEL PRESSURE: Fuel pressure regulator could be faulty causing dripping injectors if it is pressurizing the system to highly otherwise the engine would always be running rich causing increased fuel consumption.
FAULTY FUEL PRESSURE REGULATOR: Can cause dripping injectors which can cause hard starting since the motor has essentially flooded itself as fuel could get past the fuel injectors when the engine is off. Fuel could leak into the intake manifold causing a rich mixture. This could help during cold starts like a choke but hinder the ability for hot starts.
FLASH CODES (WS2)
The task to be done was to bring up what is known as flash codes, this is when the check engine light will flash in different amounts of time to bring up a number which is related to a sensor. For example the check engine light could flash 3 times then pause then flash another 5 times, this would relate to the code 35 which would then be checked against that vehicles manual to see what sensor the code relates to.
http://codinghorror.typepad.com/.a/6a0120a85dcdae970b0128776ffac2970c-pi
The vehicle that I bought up the flash codes on was a 1997 Mitsubishi Legnum, to bring up the flash codes the pin 1 on the DLC (Data Link Connector) had to be earthed out using an earthing wire which was earthed onto the chassis of the car then to the key to ignition. The DLC was located under the steering wheel but this varies for different cars some can be found under the bonnet or on the passenger side.
Once pin 1 on the DLC had been earthed out the flash code that I got was 23 which was the camshaft position sensor. After doing a visual inspection of the camshaft position sensor I found that there was a grease build up on the connector which would cause a weak signal to be sent to the ECU, after the grease and dirt was cleaned off of the sensor and connector, the engine was started and the check engine light went out indicating that the voltages sent to the ECU where now fine. This meant that the fault had been fixed.
To clear the codes the battery was disconnected for 30 seconds, this discharges the capacitors and wipes the memory of any codes in the ECU. Once this has been done the system was rechecked for codes by earthing out pin 1 on the DLC. There where no codes in the ECU which was indicated by the check engine light flashing continuously indicating no codes.
The faulty camshaft position sensor would have affected engine operation by the engine missing intermittently as it does not know when to fire the fuel injectors or the spark plugs so the ECU does not fire them until it gets a signal. If the sensor was really bad and sent no voltage to the ECU, the engine would start as the ECU would not know when to fire the injectors or the spark plugs.
Once the fault codes have been cleared, other sensors should be checked to make sure that other faulty sensors are causing problems that the ECU is not logging as a fault, this could include testing the throttle position sensor, or the air flow/pressure sensors. Anything that could cause the engine to intermittently miss or run rough.
This is one of the ways that you can check the engine for faults.
Fuel injection opening pulse Injector 0.5 milli seconds
Transmission select position Manual gearbox neutral N/A
Vehicle Speed 0 km/h
oxygen sensor 02S 703 millivolts
Idle control IAC 41 duty cycle
barometric pressure pressure sensor 99.0 kPa
This live data feed is very useful in engine diagnostics as it allows for you to look at many different sensor outputs at one time, and look for a problem which may be affecting other sensors outputs. The live feed also saves time against checking each individual sensor to try and find a problem. However Parameters or specifications are needed when using the live data feed or else all the information would mean nothing as you need specifications to make sure that each sensor matches this and that the sensors are not giving incorrect readings.
After the live data feed results had been checked it was time to check the ECU for trouble or faults codes, this is done by selecting the diagnosis or scan part of the scan tool, the scan tool then reads the ECU and brings up the code which was 23 and the component which was the camshaft position sensor, this was here because the signal voltage was to low causing the engine to intermittently miss. This fault was then cleared using the scan tool, this is done by clicking clear codes on the scan tool.
After this was done the lecturer then put a fault in the system for us to find, the fault that we got was fault code 12, Mass Air Flow sensor, and the condition was no reference voltage to the ECU. Then looking at the live data feed we had to look and see what changed, the main thing was engine load the sensor output was 0 volts as opposed to 1.33 volts. The engine RPM was lower at 874 RPM, those where the two main changes. After doing this then a visual inspection of the engine bay was done, and I found that the MAF sensor connector had been disconnected. So to repair the fault the connector was plugged back in again and the live data feed was checked to make sure that the sensors where working as normal which they where.

http://chinagrabber.com/images/products/detail/Chinagrabber_Car_Scan_Tool_SC69_02.jpg
Next the fault codes had to be cleared this can be done by disconnecting the battery for 30 seconds to let the capacitors discharge or the fault codes can be cleared by using the scan tool to clear them by clicking on clear codes. Now the system is rechecked for codes, by clicking on scan car on the scan tool, no codes where found which meant that the problem had been fixed.
The scan tool can help aid in engine diagnosis by using the live feed to look at all the different sensors of the engine and make sure all of them are working correctly. And by using the scan tool to check codes and having it tell you what sensors or actuators are not working properly. But if the ECU is not logging a faulty sensor a fault, then you can use the live data feed and parameters to make sure that all the sensors and actuators are working as they should.
This is one of the ways you can check EFI(electronic fuel injection) motors for faults.
Once pin 1 on the DLC had been earthed out the flash code that I got was 23 which was the camshaft position sensor. After doing a visual inspection of the camshaft position sensor I found that there was a grease build up on the connector which would cause a weak signal to be sent to the ECU, after the grease and dirt was cleaned off of the sensor and connector, the engine was started and the check engine light went out indicating that the voltages sent to the ECU where now fine. This meant that the fault had been fixed.
To clear the codes the battery was disconnected for 30 seconds, this discharges the capacitors and wipes the memory of any codes in the ECU. Once this has been done the system was rechecked for codes by earthing out pin 1 on the DLC. There where no codes in the ECU which was indicated by the check engine light flashing continuously indicating no codes.
The faulty camshaft position sensor would have affected engine operation by the engine missing intermittently as it does not know when to fire the fuel injectors or the spark plugs so the ECU does not fire them until it gets a signal. If the sensor was really bad and sent no voltage to the ECU, the engine would start as the ECU would not know when to fire the injectors or the spark plugs.
Once the fault codes have been cleared, other sensors should be checked to make sure that other faulty sensors are causing problems that the ECU is not logging as a fault, this could include testing the throttle position sensor, or the air flow/pressure sensors. Anything that could cause the engine to intermittently miss or run rough.
This is one of the ways that you can check the engine for faults.
SCAN TOOLS (WS5)
The task to be done was to check for fault codes logged on the ECU using a scan tool. A scan tool is a tool which reads the codes on the ECU and tells you exactly what component has been logged as a fault. The scan tool can also give live data feed, this is where it tells you exactly what voltage or reading different sensors are getting, what the engine rpm is doing and many other things which is very useful for engine diagnostics.
The first thing to do was to select the vehicle that you wanted to scan, the selection of vehicles is given to you before you do anything else with the scan tool in my case I selected Mitsubishi.

The first thing to do was to select the vehicle that you wanted to scan, the selection of vehicles is given to you before you do anything else with the scan tool in my case I selected Mitsubishi.
http://ts2.mm.bing.net/images/thumbnail.aspx?q=1264315473165&id=84dd3886fd892782beb0046c2b46c13a
The live data feed on the scan tool gave me the following data for my 1997 Mitsubishi Legnum when the engine is at idle.
PID=Parameter Identification Letters to describe Value of Data Units of data
Engine load MAF 1.33 volts
Engine RPM crank sensor 968 RPM
Throttle Angle TPS 624 milli volts
engine coolant temp. ECT 71 degrees celcius
intake air temp. IAT 26 degrees celcuis
Fuel injection opening pulse Injector 0.5 milli seconds
Transmission select position Manual gearbox neutral N/A
Vehicle Speed 0 km/h
oxygen sensor 02S 703 millivolts
Idle control IAC 41 duty cycle
barometric pressure pressure sensor 99.0 kPa
This live data feed is very useful in engine diagnostics as it allows for you to look at many different sensor outputs at one time, and look for a problem which may be affecting other sensors outputs. The live feed also saves time against checking each individual sensor to try and find a problem. However Parameters or specifications are needed when using the live data feed or else all the information would mean nothing as you need specifications to make sure that each sensor matches this and that the sensors are not giving incorrect readings.
After the live data feed results had been checked it was time to check the ECU for trouble or faults codes, this is done by selecting the diagnosis or scan part of the scan tool, the scan tool then reads the ECU and brings up the code which was 23 and the component which was the camshaft position sensor, this was here because the signal voltage was to low causing the engine to intermittently miss. This fault was then cleared using the scan tool, this is done by clicking clear codes on the scan tool.
After this was done the lecturer then put a fault in the system for us to find, the fault that we got was fault code 12, Mass Air Flow sensor, and the condition was no reference voltage to the ECU. Then looking at the live data feed we had to look and see what changed, the main thing was engine load the sensor output was 0 volts as opposed to 1.33 volts. The engine RPM was lower at 874 RPM, those where the two main changes. After doing this then a visual inspection of the engine bay was done, and I found that the MAF sensor connector had been disconnected. So to repair the fault the connector was plugged back in again and the live data feed was checked to make sure that the sensors where working as normal which they where.

http://chinagrabber.com/images/products/detail/Chinagrabber_Car_Scan_Tool_SC69_02.jpg
Next the fault codes had to be cleared this can be done by disconnecting the battery for 30 seconds to let the capacitors discharge or the fault codes can be cleared by using the scan tool to clear them by clicking on clear codes. Now the system is rechecked for codes, by clicking on scan car on the scan tool, no codes where found which meant that the problem had been fixed.
The scan tool can help aid in engine diagnosis by using the live feed to look at all the different sensors of the engine and make sure all of them are working correctly. And by using the scan tool to check codes and having it tell you what sensors or actuators are not working properly. But if the ECU is not logging a faulty sensor a fault, then you can use the live data feed and parameters to make sure that all the sensors and actuators are working as they should.
This is one of the ways you can check EFI(electronic fuel injection) motors for faults.
OXYGEN SENSORS (WS6)





The task to be done was to measure the oxygen sensors output or readings under different engine conditions and loads.
The zirconia type oxygen sensor works by measuring the amount of oxygen atoms passing through the zirconia element. The oxygen sensor produces its own voltage by doing this, it works like this, when the engine runs rich there is low levels of oxygen in the exhaust, this means that there is a high level of migration of oxygen atoms causing a high voltage of up 1 volt. When the engine runs lean there is a high level of oxygen in the exhaust so there is a low migration rate of oxygen atoms through the element which means there is a low voltage down to 0.1 volts. This is basically how a oxygen sensor works.

http://www.boschsparkplugs.net/images/pic_sensor.jpg
The first thing to do was to locate the position of the oxygen sensor, on the Toyota 1zz motor the oxygen sensor is located after the exhaust manifold but before the catalytic converter. There is usually another oxygen sensor located after the catalytic converter (cat) to make sure that cat is working properly and cleaning up the emissions.
The next check was to count how many wires the oxygen sensor has and what each wire does, the oxygen sensor we where testing had 4 wires 2 where white one of which was the heater positive and the other was heater negative or earth. Another wire was black, and that was the signal out wire and the grey wire was the signal earth wire.
The type of oxygen sensor we where working with was the zirconia narrow band oxygen sensor which operates from 0.1 to 0.9 volts.
The first test to do was to back probe the oxygen sensor signal out wire and measure the signal with an oscilloscope whilst the engine is revving at 2500 RPM.

The reading we got can be seen above, this is a good reading as it shows the oxygen sensor cycling between 0.1 and 0.9 volts or rich and lean. A bad reading would be one where there could be sudden drops at regular intervals, this would indicate an engine misfire and trick the ECU into thinking that the engine is running lean and it would make the engine run richer which would increase engine power.
Then we had to count the number of cross counts, or times it goes from low to high in 10 seconds, which was 30 times, this is a good reading as it shows that the oxygen sensor is responding quickly to changes in fuel quantity. If there where less cross counts this could indicate a sluggish 02 sensor and it would not be accurately telling the ECU what the fuel quantity is so the ECU would never be able to run the engine properly as it is never getting whether the engine is running rich or lean at the correct moment so this could cause the engine to run roughly.
The next test was to make the 02 sensor enter closed loop by revving the engine at 2500 rpm then make the engine run lean by suddenly decelerating.

The 02 sensor can be seen running on closed loop then suddenly the voltage drops off as it runs lean, this is a good reading as it shows that the 02 sensor can pick up that the engine is running lean. A bad reading would be one where the voltage may flatten off at 0.3 volts, this would tell the ECU that the engine is not running as lean as it actually is and the ECU would not inject enough fuel as it believes it is running richer than what it actually is and this would make the engine be slightly lacking in power due to the lean mixture.
The number of cross counts on this test was much less at only 7, this is because there are two large levelling off areas, one where the 02 sensor is indicating rich and just after when the 02 sensor is indicating that it is running lean.
The next test was to measure what happens to the signal when the engine runs rich. This is done by making the 02 sensor enter closed loop then blipping throttle to make the engine run rich.

The reading above shows the 02 sensor in closed loop, then the engine was revved up high so that the ECU would inject more fuel to make the engine run rich, this is the reading that we got. The engine runs rich for a very long time then can be seen going lean again, this is because the engine was returned to idle. The reading that we got was a good reading as it showed that the 02 sensor was able to accurately show the engine running rich and for a sustained period of time. A bad reading would be one where the 02 sensor only goes up to 0.6 volts this would tell the ECU that the engine is running leaner than what it actually is and the ECU would inject even more fuel to try and make the engine run rich, this would cause an increase in fuel consumption. This would also mean that the 02 sensor is no longer accurate and the ECU would never be able to make the engine run rich or lean properly as the 02 sensor cannot give the ECU a accurate reading.
The last reading is to measure the response time of the 02 sensor by making it enter closed loop then blipping the throttle to make to it run rich, then measure the time taken between the leanest point and the richest point on the 02 sensor.

The points that we measured from was the leanest point just after the 02 sensor exited closed loop to the riches point, this took around 1.9 seconds to do, this is an average reading and indicated that the 02 sensor is becoming a bit sluggish and is not able to quickly change its signals between rich and lean, a good reading would have been around 1/2 second. All this reading means is that the ECU is getting delayed signals and cannot be as accurate with its air/fuel ratio as it should be. This would mean that the 02 sensor may have to replaced soon.
These are some of the steps that you can take to measure the readings that the oxygen sensor is sending to the ECU and whether it is good or bad readings that the 02 sensor is giving.
Overall excellent work. Just be carefull when doing your response time for the O2 sensor. It doesnt have to be from the leanest point to the richest point. Just the time taken to go from one point to the other.
ReplyDelete